(Post by John Miller, SPCT)
“What book should I read next?” I have been asked this question many times. There is an easy answer and a much more in depth answer. The first is merely read the books in your field of knowledge others are reading. The second requires that we know enough about a person to mentor them in their own unique current place in work and in life. This requires much more in depth thinking and thus a unique answer.
“Not all readers are leaders, but all leaders are readers.” John Maxwell, Leadership 101.
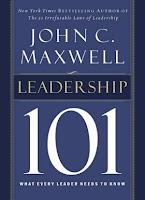
In Leadership 101 Maxwell writes that we should spend 80 percent of our people development time with the 20% of the Leaders in the organization that will make the most difference. 80% of the difference. This comes out in his 4th level (of 5 levels) of leadership. By the way, there IS a difference between a Leader and a Manager. And I’ll leave that for another note to all of you.
In Maxwell’s Level 4: People Development, he states people follow you because of what you have done for them. Individually. Not collectively. This means we know each person. And we know them well. They trust us as leaders. They have become loyal, and this is reflected in their trust.
So when someone that trusts me asks for what they should read next I take their request seriously. Yet we need to have a shared understanding. A shared language. A shared vision (that is coming from me as a leader). This also means we know where they are at. What they are doing. What books they have read. What information they need next.
I was asked a question by a really smart SPC I work with today. One that is doing all of the right things. One I really admire. It is a simple question - “What book should I read about lean budgets?” I just knew they had read all of the articles behind the icons at the SAFe (Scaled Agile Framework) site. And I was thinking they had read that initial list of books - as all of you have, correct? So what would I recommend next? I knew they were waiting, and as the milliseconds ticked by, I was thinking - I had to come up with an answer. Fast. So I was pretty quick to reply with the answer a question with a question technique.
Have you read, “… by … yet?”
The answer kind of surprised me as this is one of the short list of books listed in Lesson 7 – “Leading a Lean-Agile Enterprise” of the SPC Implementing SAFe class. Well it is in v4.5.1 anyway. I told them I was surprised they had not read it, but to read that one next. And then we had a nice discussion on what to expect to learn from this one book on lean budgeting.
My question of you is this. Are you a Level 4 Leader? Are you working with the 20% of Leaders in your organization that will make 80% of the difference? For you to have a shared understanding of where the folks putting the framework together are coming from have you read the books on that list? And if you have, have you also read the technical books in the “Sustaining and Improving” lesson (lesson 16). As a Level 4 Leader, when you’re thinking of recommending a next book from all the books you can recommend from, I challenge you to think of these questions first.
Where is this future Level 4 Leader (and maybe even Level 5 Leader) at? What books have they already read? What books do they need to read to advance their Leadership skills? Have they read the short list of books in the SPC training guide, or do they think the books on that list are just to have a reading list in the course materials. And if I have not, which one would my mentor suggest to them. Hmmm... Give the person you are mentoring a call. They might have some questions for you on the next book you might consider recommending them to read.
An ending thought.
Sometime ago one of my mentors suggested to me I had no right to recommend a book I had not read myself. Since that time I have followed his advice. I recommend this same approach to you. It will rapidly advance your own learning.
![]() |
A side picture of notes from my "DevOps Handbook", a book I frequently recommend. |